
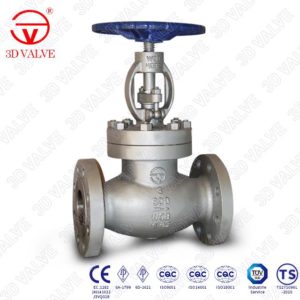
Carbon steel globe valve is forced sealed valve, valve closure, must be applied to the disc pressure to force the sealing surface does not leak.
Email-us info@tawajodindustrial.jo
Carbon steel globe valve is forced sealed valve, valve closure, must be applied to the disc pressure to force the sealing surface does not leak. When the medium enters the valve body from below the disc, the resistance to be overcome by the operation force is the friction force between the stem and the packing and the thrust force produced by the pressure of the medium, so the valve stem diameter to be large, the valve stem bending will occur.
Carbon steel is used in higher temperature, or concern with thermal or mechanical shock is an issue, which makes them popular in the oil and petrochemical industries.
Body and bonnets are high quality cast and afterwards precisely machined, directing the attention to prevent stress concentration.
Bonnets are made either of one piece only-the yoke then being an integral part of it-or have two pieces, depending on the size of the globe valve. This ensures the perfect alignment with the body what leads to an accurate opening and closing.
Bodies of globe valves are designed considering the same characteristics as gate valves, which in this case means that disc is guided in bigger valve sizes or high pressure service in order to avoid vibrations and better seat.
The design of the body-bonnet gasket varies depending on the class of the globe valve.
Class 150 to 600 globe valves consist of a circular male-female connection with a graphite or spiral wound gasket.
Class 900 and above globe valves consist of a ring type joint.
In pressure seal designs the sealing in achieved through a gasket that takes advantage of the internal pressure of the line. The material most commonly used is high-purity graphite being located between the body and the body retainer ring.
Design Features
Design standard as per: BS1873、GB/T 12235
Generally, lift is just 1/4 of the valve seat port, ensuring a short Opening/closing time.
Only one sealing face exists on the valve body and disc.
The valve is designed as a back seat sealing structure.
Use flexible and woven graphite collaboration type packing.


Product Range
Body material: stainless steel, carbon steel, forged steel, alloy steel
Nominal diameter: 1/2″~24″
Pressure range:Class150~2500
End connection: RF, RTJ, BW
Working temperature:-29℃~560℃
Operation: Handwheel, Gear Box, Electric Actuator, etc.
Brand | 3D |
Valve Type | Carbon Steel Globe Valve |
Valve Material | Cast steel, stainless steel, special alloy, etc |
Valve Test | 100% quantity tested before delivery |
Valve Guarantee | 18 months from the date of dispatch ex works, or 12 months from date of commodity installation. |
Valve Painting | Customer request |
Valve Package | Wooden case |
MOQ | No requirement |
Valve Certificate | API 6D/CE/ISO9001/ISO14001 |
Delivery Detail | Shipped in 4 or 6 weeks after payment |
Port | SHANGHAI |
Payment Terms | L/C,D/A,D/P,T/T |
Certificate Offered | Packing List,Commercial Invoice,Test Reports and Material Certificates,Certificate of quality and quantity, Seller’s Certificate of Guarantee |
Common Materials of Valve Body and Various Materials’ Heat Treatment Analysis
There are many kinds of materials of valve body, which are suitable for different working conditions.
There are nine common materials for valve body:
1. Grey cast iron, suitable for low-pressure valves with nominal pressure PN < 1.6MPa and working temperature between – 15 ~ + 200 ℃.
2. Blackcore malleable iron, suitable for medium and low pressure valves with nominal pressure PN < 2.5 MPa and working temperature between – 15 ~ + 250 ℃.
3. Ductile iron is suitable for medium and low pressure valves with nominal pressure PN < 4.0 MPa and working temperature between – 30 ~350 ℃.
4. Carbon steel (WCA, WCB, WCC) is suitable for medium and high pressure valves whose working temperature is between – 29 ~+425 ℃. Among them, 16Mn and 30Mn are between – 40 ~+450 ℃.. They are often used to replace ASTM A105.
5. Low Temperature Carbon Steel (LCB) is suitable for low temperature valves with working temperatures ranging from – 46 ~+345℃.
6. Alloy steel (WC6, WC9) is suitable for high-temperature and high-pressure valves with non-corrosive medium at working temperature between – 29 ~+595 ℃., while WC5 and WC12 are suitable for high-temperature and high-pressure valves with corrosive medium at working temperature between – 29 ~+650 ℃.
7. Austenitic stainless steel, suitable for valves with corrosive media operating at temperatures ranging from – 196 to + 600 ℃.
8. Monel alloy, mainly suitable for valves containing hydrogen and fluorine medium.
9. Cast copper alloy is mainly suitable for oxygen pipeline valves with working temperature between – 273 ~200 ℃.
The above list is a large range of commonly used materials of valve body. Specifically, there are many different grades in each type of material, and different grades are applicable to different pressure levels. Therefore, when choosing valve body material, the valve body material suitable for working conditions should be determined according to different uses and different pressure grades.
In addition, there are titanium alloy (titanium valve), aluminum alloy (aluminum valve), plastic (plastic valve), ceramic (ceramic valve) and so on.
The heat treatment process of valve body blank is as follows according to different materials:
1. Heat treatment of gray cast iron.
In order to achieve different purposes, gray cast iron can undergo different heat treatment after casting. In the production, the heat treatment processes for gray cast iron valve body and other parts after casting are thermal aging for eliminating casting stress and high temperature annealing for eliminating free cementite. Thermal aging is a necessary process. High temperature annealing can replace thermal aging only when primary cementite exists in the structure after casting due to improper control of chemical composition and cooling rate.
2. Heat treatment of carbon cast steel.
Casting steel has large residual stress after casting. Sometimes the structure of steel castings is coarse and even superheated. All of these affect the dimensional stability of steel castings, reduce the mechanical properties of steel and are not conducive to the cutting process. In order to eliminate the casting stress, refine the structure, improve the mechanical properties and improve cutting processing, carbon steel valve body and other parts are often annealed or normalized with tempered after casting in valve production.
3. Heat treatment of austenitic stainless acid-resistant steel.
The main defect of austenitic stainless acid-resistant steel is easy to produce intergranular corrosion. Generally, some heat treatment measures can be taken to prevent the corrosion. In the production, the heat treatment processes commonly used for parts such as austenitic stainless acid-resistant steel valve body are solid solution treatment (quenching), stabilization treatment and cryogenic treatment.
4. Heat treatment of martensitic heat-resistant steel.
After casting, martensitic heat-resistant steel should be annealed in time to prevent cracks, and the annealing holding time should be sufficient (generally 4-8 hours). The purpose of annealing martensitic heat-resistant steel is to eliminate stress, recrystallize, refine grain size, reduce hardness, improve cutting performance, and prepare for final heat treatment.
The final heat treatment of martensitic heat resistant steel is normalized and tempered.
5. Heat treatment of high quality carbon steel.
The heat treatment of high quality carbon steel takes 35 forged steel valve body as an example. After forging, the 35 steel valve body should be normalized, and the final heat treatment should be carried out according to the requirements of the valve manufacturing technical documents, and generally the quality control should be carried out.